Blog: Industry
Using a LIMS for Quality Control in the Mining Industry
16th February 2021
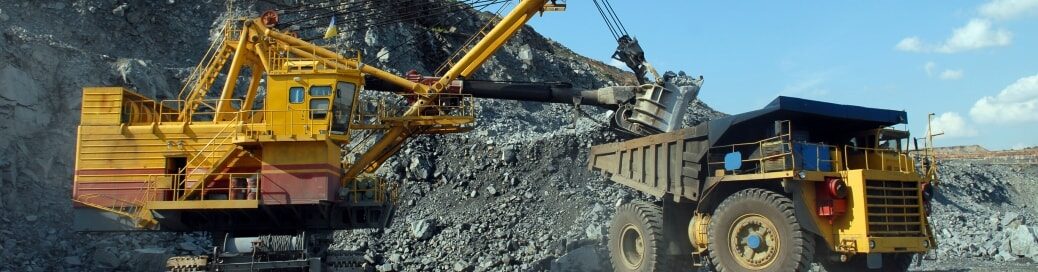
Electric vehicles and wind turbines are fast becoming part of our everyday lives. In the UK registration of battery electric vehicles in 2020 doubled over 12 months, while on average wind energy provided 20% of the UK’s power needs (National Grid) and peaked at over 50% during recent storms. This is surely good news given our insatiable appetite for energy. But what is not so widely known is that the generators within wind turbines require rare earth metals in their permanent magnets (including neodymium, terbium, and dysprosium,) to vastly improve their efficiency. Electric vehicles contain similar material in their motors. Other rare earths such as lanthanum and cerium, as well as lithium, are present in the batteries of electric vehicles.
This growing need for rare earth metals and other elements has put a new focus on mining. Former, tin mines in Cornwall, for instance, are being re-opened to extract lithium, while traditional mining activities are as important as ever. Whether it be coal or uranium for power generation, metals such as gold, copper, and iron ore or potash for agricultural fertilizers, all seem to be in increasing demand in this modern world while pressure on the environmental impact of their extraction increases.
Electric vehicles and wind turbines are fast becoming part of our everyday lives. In the UK registration of battery electric vehicles in 2020 doubled over 12 months, while on average wind energy provided 20% of the UK’s power needs (National Grid) and peaked at over 50% during recent storms. This is surely good news given our insatiable appetite for energy. But what is not so widely known is that the generators within wind turbines require rare earth metals in their permanent magnets (including neodymium, terbium, and dysprosium,) to vastly improve their efficiency. Electric vehicles contain similar material in their motors. Other rare earths such as lanthanum and cerium, as well as lithium, are present in the batteries of electric vehicles.
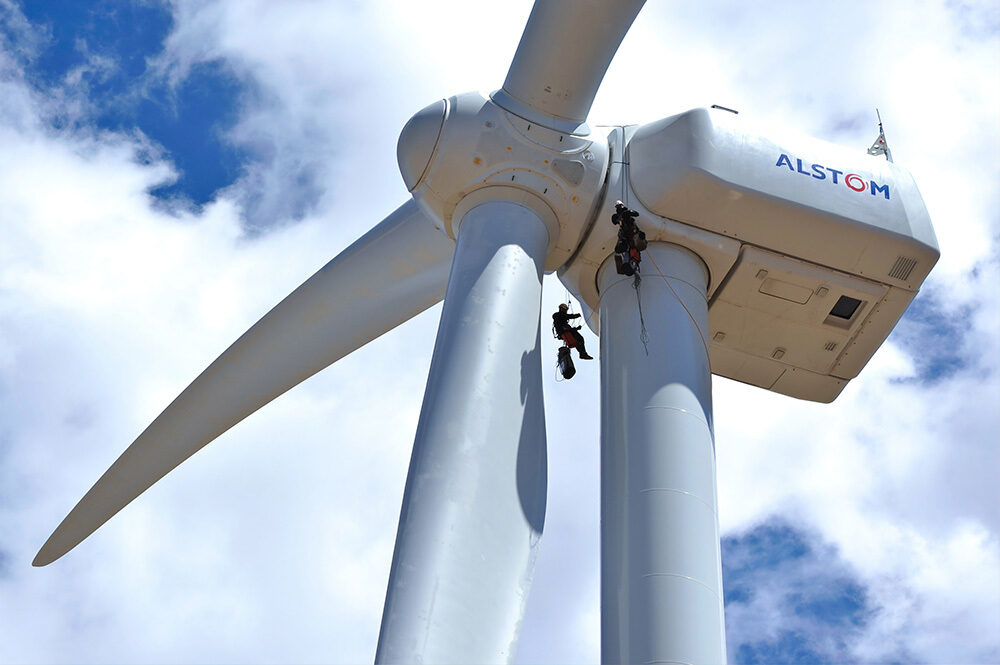
This growing need for rare earth metals and other elements has put a new focus on mining. Former, tin mines in Cornwall, for instance, are being re-opened to extract lithium, while traditional mining activities are as important as ever. Whether it be coal or uranium for power generation, metals such as gold, copper, and iron ore or potash for agricultural fertilizers, all seem to be in increasing demand in this modern world while pressure on the environmental impact of their extraction increases.
Delivering Consistent Quality
While some materials, such as coal, will not need refining, others including gold and rare earth elements will need extensive processing to recover the material of interest.
Raw (freshly mined) material will have differing percentages of the desired material within it depending on the purity of the seam being mined. This leads to a requirement to grade the material according to quality and, often, a requirement to mix different streams of material to get the required level of purity. In this case the production laboratory provides quality assurance for the raw material, issuing a certificate of analysis to verify its purity.
Where refining activities take place at the mining site the QC lab can be responsible for ensuring quality throughout the refining process. Where processing is done off site a different lab may do this testing; this facility may also be responsible for confirming the purity of the delivered raw material or for ensuring that the purity is confirmed by an independent organization.
A LIMS in a production laboratory must therefore be able to assay the material, grade it and provide certificates of analysis to accompany each batch. The lab may use an array of instruments, many of which can and should be connected to the LIMS to automatically record the results of each assay. This reduces errors and increases the efficiency of the laboratory.
Environmental Monitoring
While mining is an indispensable part of the global economy there is growing concern over its environmental impact and therefore a growing demand to monitor, record and report any possible contamination. LIMS cannot only record the results of such testing but using an Environmental Monitoring application it can map where the sampling should take place, the frequency of testing and trend results over time.
Requirements of a LIMS in mining
Combining the requirements of mining exploration and production, the key elements of a mining LIMS include ability to:
- Integrate with laboratory instruments
- Store and retrieve batch related assay results
- Provide certificates of analysis
- Compare results to determine variation in quality over time
- Drive cGxP standards including staff competency and documentation
- Manage laboratory inventory
- Grade batches for specific customer needs or country standards
- Comply with cGxP and similar laboratory standards
- Oversee quality control with the use of blanks, duplicates, and reference standards
- Define and manage environmental monitoring regimes
If production includes refining the material, or similar steps, then the predefined manufacturing LIMS may be the best system to start from, since this builds in the ability to handle raw, intermediate, and final product. If this is not the case a QC/contract laboratory flavor of LIMS may be the best system to start from. Defining the system requirements and discussing those with Autoscribe will quickly provide the answer as to which is the best starting point for your mining LIMS.
Whatever Matrix Gemini LIMS starter configuration you use the underlying software will be exactly the same. Configuration of the screens and workflow is completed using the built-in graphical configuration tools. Each customer’s unique configuration is stored within the database, separate to the software, enabling an easy support and upgrade path. Customers may even configure their own screens should they wish. Autoscribe offer a three-day training course to train users to configure their own solutions, enabling them to tweak the system themselves as needs evolve.
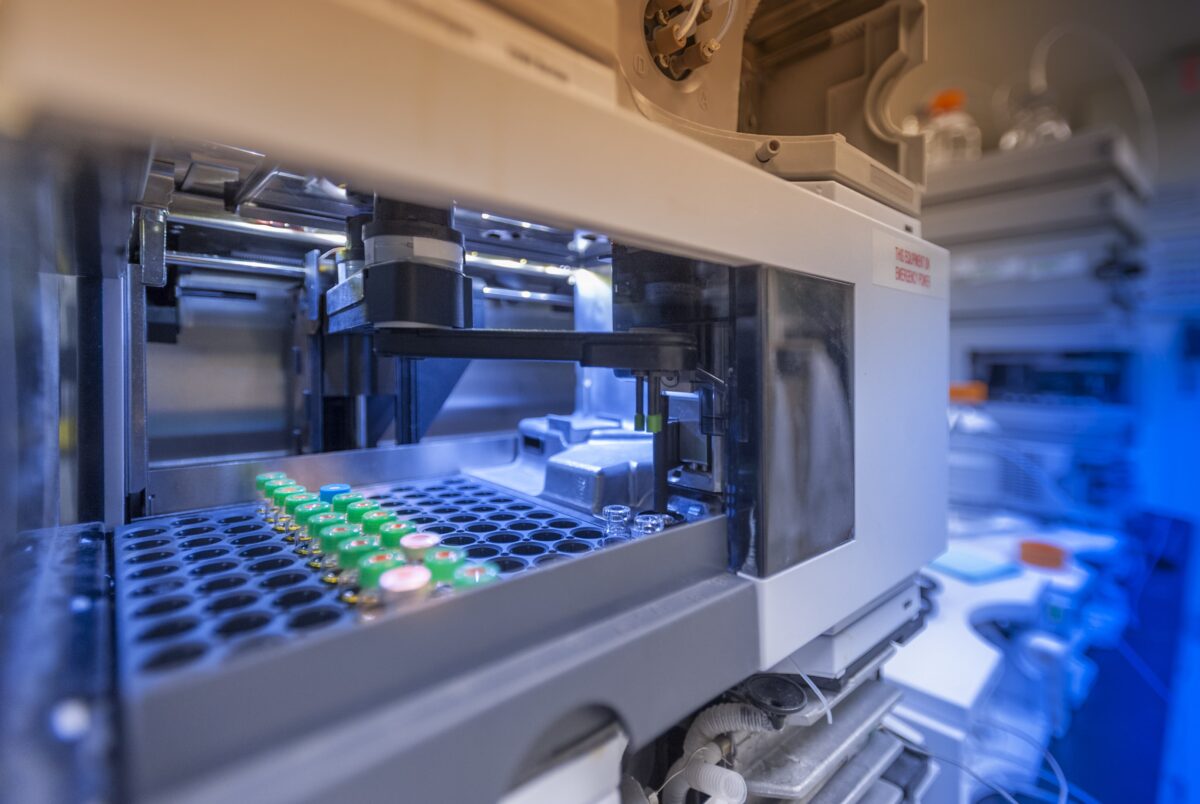
A LIMS is critical to mining operations since they ensure that the delivered product is of a guaranteed quality. With the increasing use of electric vehicles, wind turbines, electronics, and similar modern technology, exploring, mining, and refining rare earth elements has given the mining industry a new dynamism which is set to continue while traditional mining operations remain vital to the global economy.
Further Research
Autoscribe Informatics have a number of customers in the mining and related industries who use Matrix Gemini LIMS as an integral part of their laboratory QC function. One typical customer, a world leader in nickel mining, uses the LIMS to provide sample analysis for process control, final product quality and for environmental checks. Shipment certification now happens in minutes and results are no longer mislaid. They remarked “One of the most satisfying results of the switch to Matrix Gemini LIMS was that our technologists were very happy with the new system and often commented on how much time Matrix saves them in their day-to-day work”. You can download the mining LIMS QC case study here.
For further information on the Matrix Gemini LIMS for mining operations please download the brochure from the materials, metals and mining LIMS industry page or contact us.