Blog: Business
Is your laboratory fit for purpose?
29th November 2016
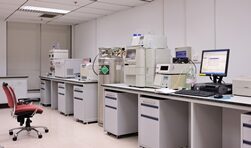
One of the many key factors in ensuring that a laboratory is fit for purpose is to make sure that all the analytical instrumentation and equipment is not only operating within specification, but also that it is being properly maintained and serviced according to the manufacturers’ recommendations. One way of managing this requirement is to keep computerized records of the operational status of each piece of equipment.
By linking this data through the LIMS, it can provide immediate feedback on instrument availability when a particular analysis is scheduled, rather than checking the status when the results need to be entered. This prevents the allocation of work to an un-calibrated instrument or one that has not been maintained correctly. There are plenty of other benefits, since such a system can also keep a record of all instruments within the laboratory together with a history of all maintenance events for audit purposes, provide reminders of pending calibration and maintenance tasks and allow assessment of instrument support agreement value. These in turn ensure the laboratory can demonstrate that it follows standard calibration and maintenance procedures and even indicate which instruments are most costly in terms of maintenance and reliability.
Key management data
All the key management data can be recorded using Autoscribe Informatics’ Instrument Calibration and Management System (ICMS) which is available as an option within the Matrix Gemini LIMS or as a standalone product. Three types of data are usually recorded in order to allow the instrument status to be determined: instrument details, calibration and maintenance information.
Instrument details
Typical instrument details that can be recorded include description, manufacturer, model number, serial number, location, responsible user, warranty information and support contract price (with tracking of renewal dates) and much more. Component level tracking e.g. for HPLC systems, is also possible. Lists of spares and consumables with current part numbers, suppliers and costs can be added and linked to the appropriate instrument/ equipment record as needed and this allows overall instrument running costs to be calculated.
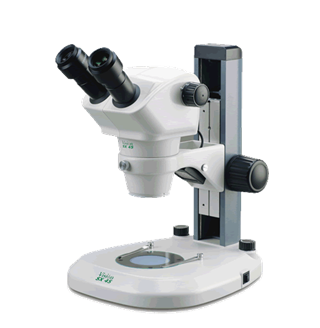
Calibration details
Details on calibration include scheduling of calibration intervals (by usage rate or by time) and the permitted instrument calibration limits. Actual calibration results are checked automatically against these limits and out of limit results will be flagged with the instrument status automatically changed to unavailable. There is also provision to record any comments.
Maintenance details
This covers the various aspects of instrument maintenance including the scheduling of routine maintenance/ inspection intervals according to manufacturer’s recommendations. In addition, all faults, breakdowns and non-routine occurrences can also be recorded. By showing the time, date, user and description of the problem, all maintenance issues can be tracked. Especially useful for portable or ‘signed-out’ items is the ability to record the location where equipment was in use when a maintenance issue oocurs. Comments can be entered for each maintenance event.
Using the information
ICMS allows instrument status to be tracked automatically as to whether it is available or unavailable and identifies events such as the maintenance period being exceeded etc. An automatic change of status occurs when calibration or maintenance is overdue and when it is performed. Automatic reminders of scheduled events are provided. As well as flagging events that affect the availability of instruments, the system can produce a series of useful reports:
- An instrument inventory together with calibration and maintenance schedule
- A list of instruments due for calibration over the next user specified period
- A list of instruments due for a maintenance event over the next user specified period
- All overdue calibrations
- All overdue maintenance events
- All unavailable instruments
- Instrument labels
It is also possible to develop additional reports using Crystal Reports or other reporting tools. ICMS – yet another tool from Autoscribe Informatics to help ensure that a laboratory is fit for purpose!